Underwater inspections done faster, safer and more cost-effective
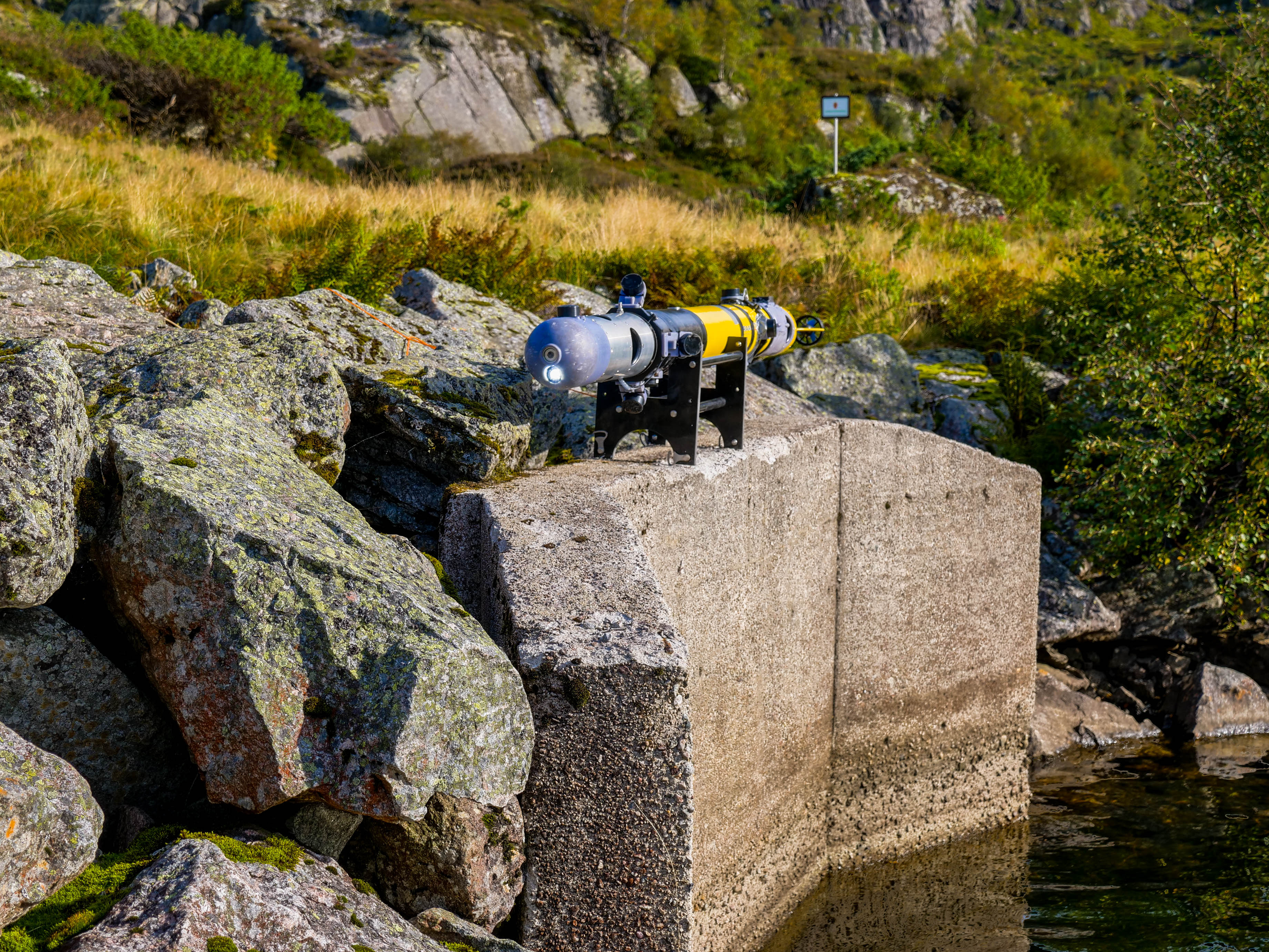
Portable, Autonomous, and Eco-Friendly
Our mission
SASSAS aims to set a new standard for underwater inspections and surveys by delivering autonomous solutions that enhance safety, reduce downtime, and minimize environmental impact. We aim to make inspections faster, safer, and more cost-effective for industries that rely on submerged assets.
What we do
SASSAS specialize in underwater robotics and autonomous technology, focusing on inspections in water-filled environments such as tunnels, pipelines, dams, and other confined spaces. Our Autonomous Underwater Vehicles (AUVs) provide high-resolution, accurate, and efficient inspections, capable of navigating even the most challenging underwater conditions.
The data collected during inspections is processed into a high-resolution 3D point cloud, offering comprehensive analysis to empower informed decision-making with confidence. Reduce inspection time, lower costs, and safeguard the integrity of your assets with precise, reliable data tailored to your needs.
Underwater Tunnel Inspections
Our advanced AUV technology delivers unmatched accuracy and safety in tunnel inspections, eliminating the need for manual entry or dewatering. By operating autonomously, the AUV mitigates risks like tunnel collapses and minimizes stress on aging infrastructure, all while preserving natural water conditions.
Effortless and Eco-Friendly Solutions
Ideal for submerged, hard-to-reach structures, the AUV safely inspects tunnels, spillways, and pipelines without disrupting the environment. Its untethered, autonomous operation allows for fast, thorough inspections, providing reliable results in even the most sensitive or remote locations.
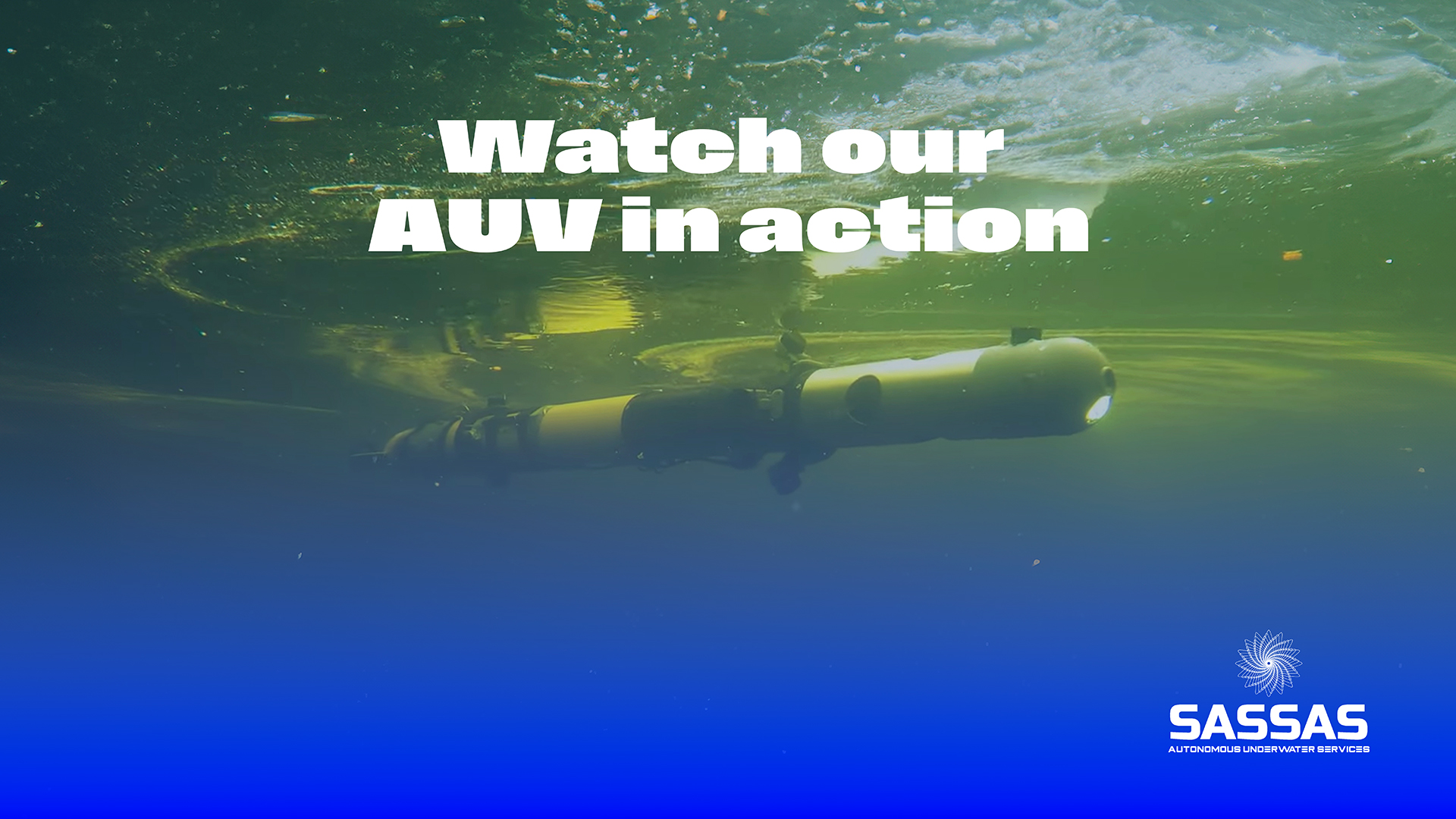
Inspect tunnels smarter – not harder!
In collaboration with our trusted technology partner, we leverage advanced autonomous navigation systems to deliver precise and efficient underwater inspections.
Technology Advantages:
No Dewatering or Tunnel Drainage Required
Unlike manual inspections that involve draining tunnels or pipelines, our AUV operates fully submerged, eliminating the risks associated with dewatering, such as
tunnel collapses or structural stress. This not only saves significant time and costs but also ensures safer inspections of your
infrastructure.
No Heavy Transportation or Cranes Needed
The AUV’s man-portable design allows it to be transported and deployed by just a small team, without the need for cranes, large transport vehicles, or extensive setup. This makes it ideal for remote locations and sites with limited access,
reducing both logistical costs and Environmental impact.
No Cable/Tether Risks
Tethered ROVs face cable drag, entanglement risks, and restricted movement, especially in confined tunnels and underwater structures. Our AUV’s untethered, fully autonomous operation
eliminates these risks, enabling it to navigate narrow, complex spaces with ease.
Minimal Environmental Footprint
The AUV leaves no local environmental
footprint, making it perfect for inspections in sensitive ecosystems and natural areas. With no heavy equipment, dewatering, or invasive procedures, the AUV ensures that the surrounding environment is undisturbed during operations.
Cost Savings
With faster deployment, no need for dewatering, reduced downtime, and fewer personnel requirements, our AUV technology offers significant cost savings compared to both traditional ROV systems and manual inspections.
Testing of AUV in Hydropower Tunnel
In a pilot project SASSAS tested its innovative technology for autonomous inspection of water-filled tunnels. Using our AUV, inspections were conducted without draining the tunnels, significantly reducing downtime.
As part of our project, we successfully tested our AUV in a flooded hydropower tunnel. The test focused on the integration of sensors and our newly developed software for autonomous navigation in signal-denied environments. The AUV was able to navigate the tunnel independently, without requiring the draining of water or the use of large machinery.
The results confirmed that our navigation software and integrated sensors functioned as expected, enabling precise and reliable operation in challenging conditions.
Contact us
We would like to hear from you!
Keep updated
We are ready to meet your interest in autonomous inspection. Join our journey and connect with us!
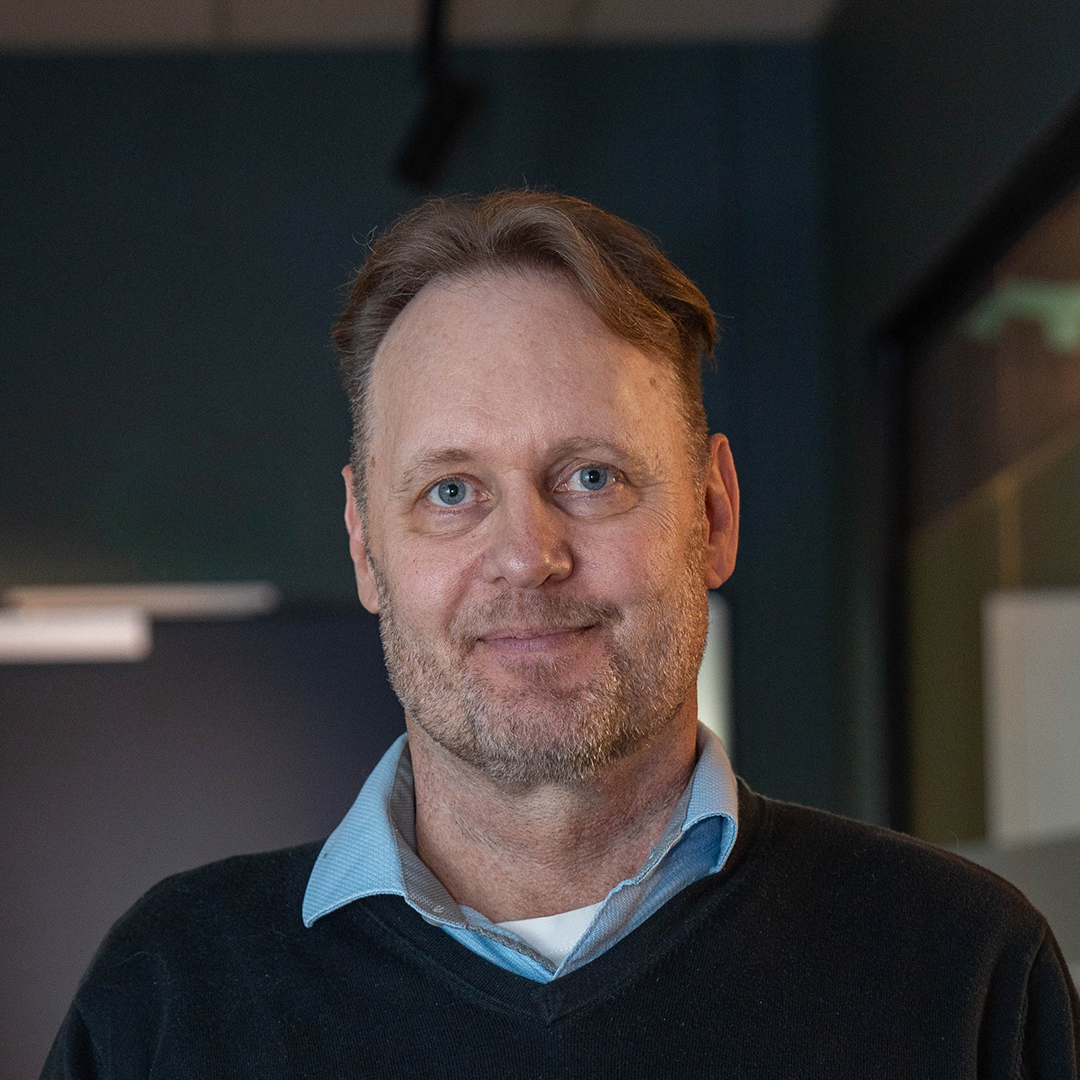
Passionate about advancing sub water inspection technology for safer infrastructure.